

Best Manufacturing ERP Software in UAE
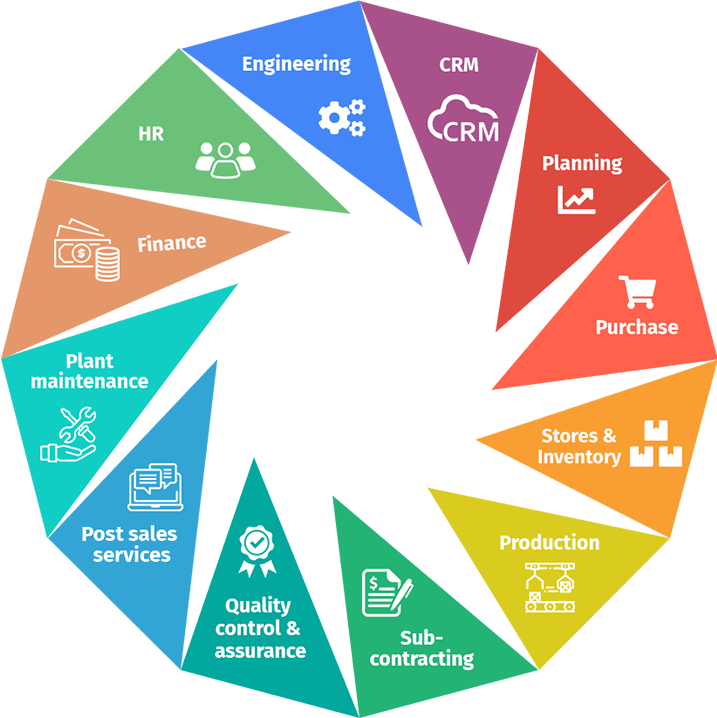
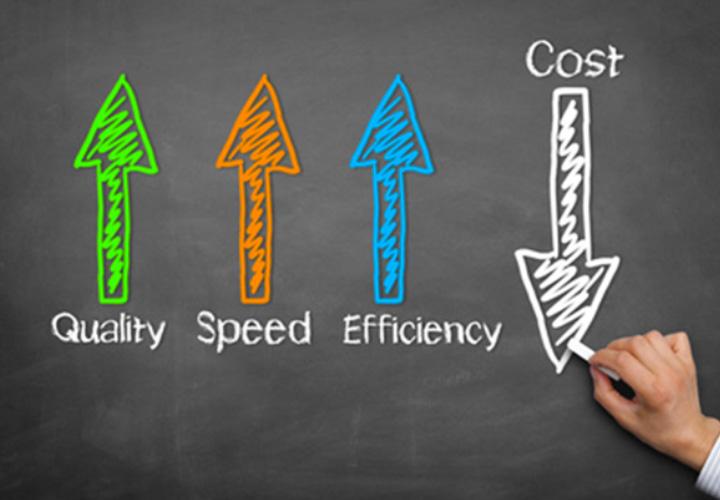
Reduce Wastage, Increase ROI.
Strategic Business Advancements with Resource Factors
Unlocking Insights for Informed Decision Making
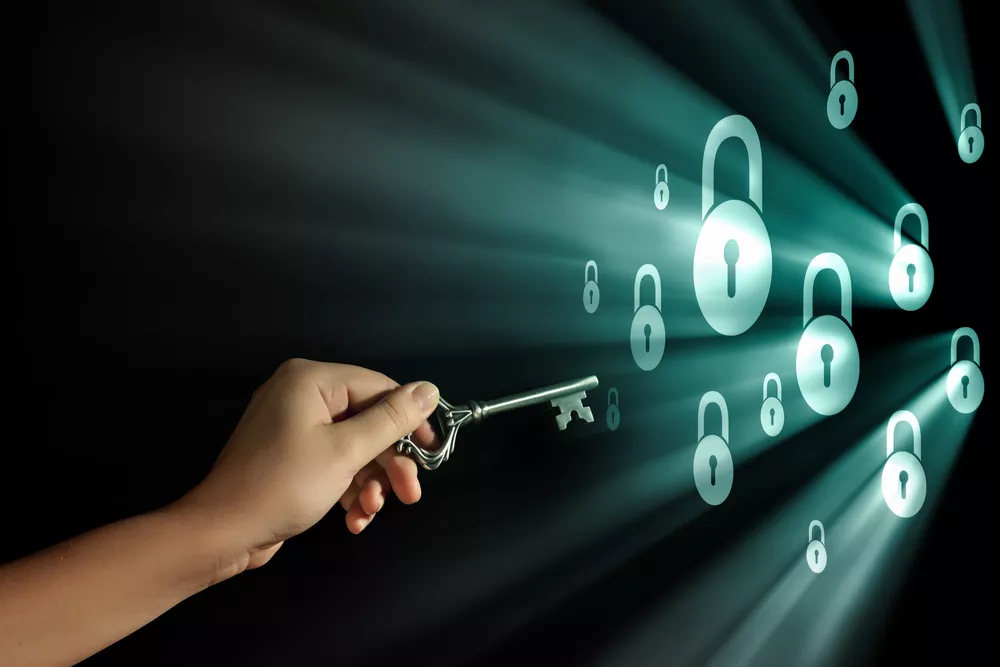
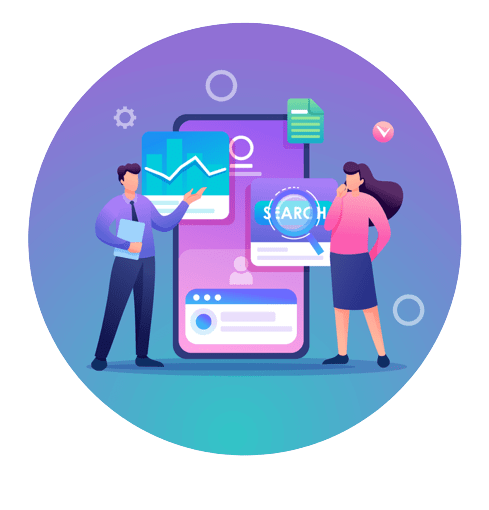
Optimization Of The Production Process

Multi-Level Bill of Materials
Define a comprehensive Bill of Materials (BOM) that includes the complete recipe of finished goods.

Workstations
manufacturing process in ERP Store essential information about the locations where workstation operations are conducted.

Quality Inspections
Implement complete quality inspections at various stages, including receiving, dispatching, and throughout the manufacturing process.

Material Consumptions
Automate the tracking of material consumption during the entire manufacturing process.

Sub-Contracting
Easily manage sub-contracted items during the manufacturing process.

Scrap Management
Effectively manage scrap, either as waste or as new inventory items.

Routing
Store all operations, including descriptions, hourly rates, operation times, and batch sizes, to streamline manufacturing processes.

Work Orders
Utilize Work Orders as documents that signal the manufacturing shop floor to produce specific quantities of designated items. Manufacturing ERP also generate material requirements.

Timesheets
Record the number of hours employees spend on each task, aiding in billable calculations, salary tracking, and project or task contributions.

Production Plans
Implement Production Plans to facilitate production and material planning for items planned for manufacturing, whether for customers or internal use.

Job Cards
Job Cards store actual production information for specific operations performed on workstations. These are created from Work Orders and guide production on the manufacturing floor.

Operations
Analyze production processes to gain valuable insights.

Production Analytics
Analysis for the production processes.

Item / Raw Materials Alternatives
Configure alternative items if needed.

Capacity Planning
Make informed decisions regarding new orders based on available resources and existing work orders.
Reports
All Of The Reports Listed Below Are Included In Manufacturing ERP Software in Dubai UAE. Besides That, Reports Can Be Customized In Order To Meet The Requirements.
.
Production Planning Report
.
Work Order Summary
.
Quality Inspection Summary
.
Downtime Analysis Report
.
Job Card Summary
.
BOM Search Report
.
Work Order Consumed Materials Report
.
BOM Stock Report
.
Production Analytics
.
BOM Operations Time Report
Transparent Cost Management
Monthly cost comparison reports break down your expenses, including direct materials, direct labor, and manufacturing overhead allocated to each job. This level of detail empowers you to make informed financial decisions and refine your operations for better cost control.
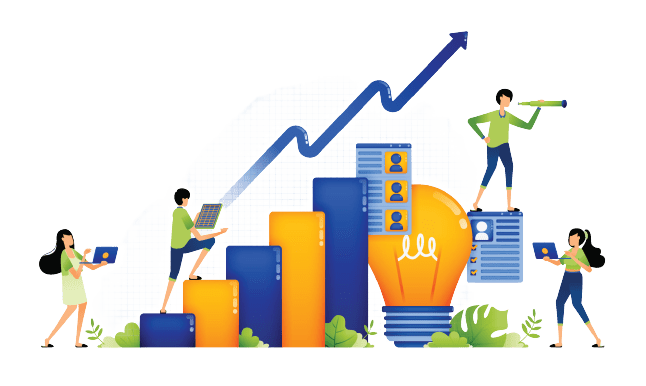
Let's Boost Your Business With Resource Factors
Key Features
.
Easily manage production based on standard formulas
.
Efficiently handle material issues and store requisitions.
.
Enter finished goods production with complete cost calculations.
.
Calculate material consumption accurately.
.
Monitor work-in-progress seamlessly.
.
Manage production based on orders.
.
Allocate labor costs accurately to each production batch.
.
Automate overhead and indirect expense distribution.
.
Gain deep insights with a detailed supplier age analysis.
.
Customize and consolidate reports in various formats for in-depth analysis.
.
Handle all aspects of order processing, including local purchase orders, open LPOs, and purchase confirmations.
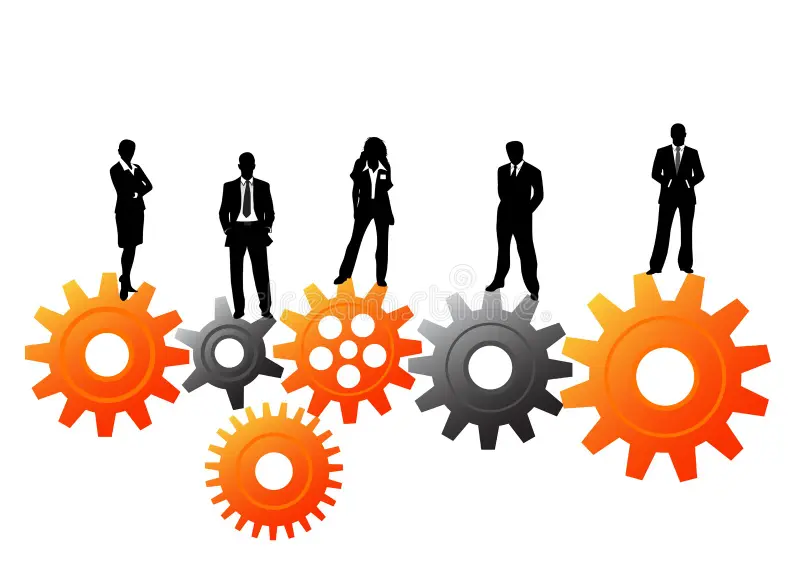
Emirates
.